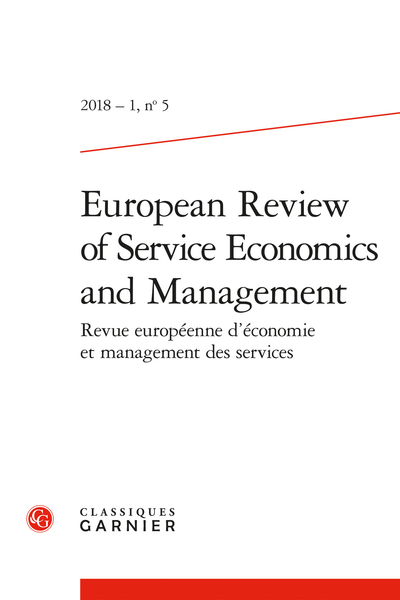
Comparer la mesure de la performance dans la maintenance industrielle et la gestion des installations
- Type de publication : Article de revue
- Revue : European Review of Service Economics and Management Revue européenne d’économie et management des services
2018 – 1, n° 5. varia - Auteur : Bröchner (Jan)
- Résumé : Les indicateurs de performance utilisés en maintenance industrielle et en gestion des installations sont différents. Sur la base du concept de coût de la mesure et d’articles de synthèse récents, cette contribution analyse les contextes organisationnels, y compris les triades de services, la servitization et les contrats fondés sur les résultats. Les différences sont attribuées à l'orientation client, à l’imprécision quant à l’état initial des ressources évaluées et à la subjectivité des évaluations de la performance.
- Pages : 45 à 63
- Revue : Revue Européenne d’Économie et Management des Services
- Thème CLIL : 3306 -- SCIENCES ÉCONOMIQUES -- Économie de la mondialisation et du développement
- EAN : 9782406080640
- ISBN : 978-2-406-08064-0
- ISSN : 2555-0284
- DOI : 10.15122/isbn.978-2-406-08064-0.p.0045
- Éditeur : Classiques Garnier
- Mise en ligne : 06/04/2018
- Périodicité : Semestrielle
- Langue : Anglais
- Mots-clés : Performance, coût de mesure, maintenance, installations, servitization, contrats
Comparing
performance measurement
for industrial maintenance
and facility management
Jan Bröchner
Chalmers University of Technology, Sweden
Introduction
One category of business services concerns operations on heavy tangible assets belonging to a client. To this category belong services linked to mobile assets, such as handled in logistics, and there are other services such as facility management (FM) and industrial maintenance (IM), both related to the client’s immobile assets. Strong reasons for a growing interest in developing schemes for performance measurement of these and similar services are the widespread practices of outsourcing, servitization and the support provided by more efficient ICT systems. Already in 2005, European large companies had outsourced almost all their facility management and a majority had done so for production (Barthélémy and Quélin, 2006). There are thus twin reasons for measuring service performance: to improve service processes and to monitor contractor activities and outcomes.
There should be lessons that facility management can learn from industrial maintenance and vice versa. By recognizing and analysing specific features of facility management and industrial maintenance, rather than attempting to generalize observations under a common umbrella 46of “business services”, opportunities for learning should be possible to identify. Therefore, the purpose of this investigation is to identify and explain similarities and differences in performance measurement for industrial maintenance and facility management.
The paper begins with an outline of how the comparison is based primarily on measurement cost reasoning. Next, the use of recent review articles and other secondary sources that emphasize the organizational context of performance measurement is presented. Three main phenomena often associated with industrial management are brought up: service triads, servitization and outcome-based contracts. Finally, the differences between performance measurement in facility management and industrial maintenance are attributed to precision of initial status documentation, range of stakeholders and the role of subjective evaluations of performance.
I. Theory and methodology
Taking two types of business services and comparing the practices used for measuring performance requires a theoretical framework that explicitly includes measurement activities. This should be particularly useful if the comparison involves the role of performance measurement in contractual relationships such as arise from outsourcing of services.
As many as nine theoretical perspectives adhered to by earlier investigators were identified by Wynstra et al. (2015) in their research agenda for service triads. Among these nine perspectives, transaction cost economics recognizes the ex post costs arising from monitoring contractual performance. Servitization as when manufacturers enter the after-sales services market can be understood as vertical integration, something which can arise from high measurement costs (Barzel, 1982). Empirical investigations of the effects of measurement costs are few, however, and mostly oriented towards IT services. In their study of IT service contracts, Argyres et al. (2007) found that “projects for which measurement is difficult also pose difficulties for developing detailed task descriptions”, which is only what can be expected. On the other hand, 47Lacity et al. (2011) have expressed doubts regarding the applicability of transaction cost economics in this context, pointing to ambiguous results from earlier empirical studies that include difficulty of measurement. Whether these doubts are valid also for other business services such as facility management and industrial maintenance–as well as for extended versions of transaction cost economics that allow recognizing the evolution of both provider and buyer capabilities (Langlois, 1992) – remains an open question.
There is no lack of studies of how to devise performance indicators, in contrast to how little interest has been generated by the existence of administrative costs of actual measurement and what the consequences of these costs might be for outsourcing and servitization. The relative ease of measurement has increased by the current availability of efficient ICT solutions, but there is still an effort involved. This is clearly so for most organizational indicators as opposed to technical indicators, since there will be more of evaluation than simple measurement (Djellal and Gallouj, 2008, 51). The increase in subjectivity when assessing people-oriented performance leads to challenges in monitoring outsourced services.
The recent ISO 41011 standard defines facility management as an “organizational function which integrates people, place and process within the built environment with the purpose of improving the quality of life of people and the productivity of the core business”. Examples of what this means in practice can be taken from the NACE Rev. 2 description of Class 81.10 Combined facilities support activities: “general interior cleaning, maintenance, trash disposal, guard and security, mail routing, reception, laundry and related services to support operations within facilities”. Industrial maintenance is classified under NACE 33.1 Repair of fabricated metal products, machinery and equipment. Both facility management and industrial maintenance include technical maintenance, and both can be understood as support services aiming to raise the performance of a core business. Although it is customary to distinguish between productivity and performance, it is unlikely that those who formulated the facility management standard took the distinction seriously.
With a focus on manufacturing related services, Lay et al. (2009) have developed a typology for business-to-business services in their 48analysis of new business concepts. They identify a set of characteristic features: ownership (during/after phase of use), personnel (manufacturing/maintenance), location of operation, single/multiple customer operation, payment model. While there are many combinations of these features in the case of industrial maintenance, facility management provided as a service over the market shows less variation in its pattern. For FM, ownership of the facilities is not transferred to the service provider; however, it is conceivable that facilities owners may retain ownership of equipment that is at least partly used by the facility management firm. As to personnel, this is clearly dominated by staff employed by the facility management contractor and its subcontractors – but some coproduction with customer staff does occur. Obviously, the location of facility management operations is at the customer’s establishment, although to take just one example, rugs may be removed for cleaning, and IT services as well as surveillance can be provided partly by systems run by remote staff. Facility management operation for multiple customers can be exemplified by commercial buildings with several office tenants who receive coordinated services.
Jaakkola et al. (2017) have devised a service typology with four clusters (routine-intensive, technology-intensive, contact-intensive and knowledge-intensive services). Facility management appears in their examples to belong primarily to their first cluster with routine-intensive services, while industrial maintenance presents features of both routine-intensive and technology-intensive services. In addition, it can be claimed that at least part of facility management services (e.g. reception) belongs to their third cluster, that of contact-intensive services. Arguably, there are also elements in both facility management and industrial maintenance that could be counted as knowledge-intensive, although not to the extent typical of the fourth cluster in the typology.
From a methodological viewpoint, this investigation is of a conceptual nature and depends on earlier research on monitoring of business services. Recently, several useful surveys of studies of industrial maintenance have been published by researchers in operations management (Simões et al., 2011), supply chain management (Karatzas et al., 2016) and marketing (Wynstra et al., 2015).
The literature on performance measurement in facility management is less extensive, with the exception of studies of effects on customer 49productivity (a theme that is seldom approached by those who investigate industrial maintenance) (Tucker and Smith, 2008; de Been et al., 2017) and of buildings-and-energy studies (Nguyen and Aiello, 2013: Lee et al., 2014). As we shall see, the emphasis is more on the performance induced by facility management activities, as opposed to industrial maintenance, where the performance focus is on the activity of maintenance in itself.
When depending on earlier published research as here, it is a risk of being misled if authors studying performance measurement in facility management tend to work within theoretical frameworks different from those typical of published industrial maintenance research. Differences in terminology may then overshadow essentially similar features of performance measurement in facility management and industrial maintenance.
II. Organizational context
of performance measurement
While the straightforward measurement of technical performance might be largely similar in the cases of industrial maintenance and building maintenance, the organizational context may show typical differences, considering performance measurement both within organizations and where several organizations are involved.
II.1. Industrial maintenance
The European standard EN 15341:2007 “Maintenance key performance indicators” synthesizes principles found in the mainstream literature on equipment maintenance. It lists economical, technical and organizational indicators, but the organizational indicators are clearly of an internal nature.
With time, the scope of maintenance has shifted from a “narrowly defined operational perspective” to an “organizational strategic” perspective, according to the literature review by Simões et al. (2011) of maintenance performance measurement. They collected 345 measures 50from the literature and identified 37 measures with more than two occurrences in the material. In the group of the least used measures, they listed “customer satisfaction”. The three frequently identified industry contexts were automotive, electrical/electronic and chemical.
Kumar et al. (2013) in their state-of-the-art review of maintenance performance metrics refer to the increased reliance on outsourcing as a reason for measurement. They also bring in a wider view of an organization’s stakeholders. Stakeholder satisfaction is classified by them as a soft indicator among leading (as opposed to lagging) indicators that may be used for predicting financial performance. Nevertheless, the strong human component of such indicators is seen as creating problems due to their lack of hard objectivity and reliability. Multi-criteria indicators reported in earlier literature covered by their review do include customer and employee satisfaction. The traditional mainstream literature is here characterized as dominated by indicators relating to equipment performance, as well as by maintenance-cost-related measures. It is obvious that inspiration from the Balanced ScoreCard has been instrumental for the development of a broader set of indicators of maintenance performance, including the customer perspective. Tsang et al. (1999) were thus inspired by scorecard principles when they brought in customer satisfaction and a few other measures in this perspective.
Again, there is also little evidence of “full reflection of organizational context” in the review of performance measurement and management two years later (Parida et al., 2015), published by almost the same group of authors (Kumar et al.) as in 2013. Indirectly, they here refer to measurement costs when acknowledging that organizations may suffer from data overload. The need for satisfying “all stakeholders” is underlined, and their review includes a number of studies published since the 1990s that include customer perspectives, customer satisfaction and customer focus. A study by Toossi et al. (2013) has revealed that maintenance customers do value specialist knowledge, accessibility of service provider, quality of equipment and of repairs as well as service orientation; the problem that remains is defining the corresponding indicators for everyday use. In general, there is a gap between industry use of maintenance indicators and their strategic relevance, as appears in a study of Belgian manufacturers (Muchiri et al., 2010).
51Although it is not clear how far industry practices in general have moved along the trend of including organizational performance indicators with a wider set of stakeholders in industrial maintenance, there is a consensus among researchers that the trend has existed for decades.
II.2. Facility management
Performance measurement models often used by facility management professionals, at least in the UK and Ireland according to Meng and Minogue (2011), include key performance indicators (KPIs), the Balanced ScoreCard (cf. Amaratunga et al., 2002; Amaratunga and Baldry, 2003) and the EFQM (European Foundation for Quality Management) business excellence model. “Client satisfaction” was found by Meng and Minogue to be the most important KPI, followed by “cost effectiveness”. When Hinks and MacNay (1999) had engaged facility management practitioners in a broad Delphi exercise in order to identify facility management KPIs, almost all the indicators were output-oriented, reflecting a client perspective.
Since the 1990s, the important fields of facility management KPIs appear to have shifted (Lavy et al., 2010). At first, the trend “was moving toward the management of maintenance activities”. Later trends suggested concentrating on sustainable energy and economic savings. Nevertheless, there remains a fundamental concern with the customer perspective. The analytical hierarchy process (AHP) has been applied to facility management KPIs in a case study of a teaching hotel (Lai and Choi, 2015). In this specific context, education support was ranked highest, and next in rank came facilities performance indicators, comprising maintenance standard, safety & security, service standard and guest satisfaction.
There are a few studies concentrating on performance measurement for building maintenance as one aspect of facility management, the aspect that is more closely related to industrial maintenance. Here, customer satisfaction has been measured relying on the SERVQUAL scale. Siu et al. (2001) found in their case study that for both clients and service providers, the reliability dimension was the most important; unlike the providers, clients “considered tangibles less important than the other three dimensions of responsiveness, assurance and empathy”. These results were not confirmed by Lai and Pang (2010) in their 52Hong Kong study of satisfaction with building maintenance; instead they found almost equal expectation gaps across all five SERVQUAL dimensions. Clearly, these divergent results indicate a dependence on maintenance context.
II.3. Service triads
It was not unusual that early studies of business services assumed a setting consisting of only a dyad of buyer and provider. For many business services, there is currently a growing interest in applying the concept of service triads, made up by buyers, subcontractors and end customers (van der Walk and van Iwaarden, 2011) or buyers, suppliers and customers, as in the overview provided by Wynstra et al. (2015).
Considering industrial maintenance, Karatzas et al. (2016) have investigated relationship determinants of performance in service triads. They analysed maintenance, repair and overhaul (MRO) contracts and in particular the performance of the manufacturer-service supplier toward the manufacturer’s customers, exploiting data from no less than 38 triads within the network of a large commercial vehicle manufacturer. Their survey included a composite service performance measure, designed as an average of KPIs with four aspects: car safety test first-time pass rate, breakdown attendance times, spare parts availability, and “a specific measure capturing each site’s responsiveness to incidents concerning vehicles under fixed-cost service contracts”. Another recent study by Pekkola et al. (2016) distinguishes between partner role stages in networked maintenance services, defining measurement targets and suggesting measures related to customer satisfaction.
Although the “service triad” term is rare in the facility management literature, the phenomenon of complex supply chains and customers’ customers is often taken for granted in the facilities context. Thus it is common to analyse the relation between users and owners of buildings as well as service providers (Kadefors and Bröchner, 2004), who often coordinate a number of service subcontractors (Jensen, 2017). Public sector organizations are important users of facility management services, be they internally managed or procured externally, and very often, e.g. for hospitals (Featherstone and Baldry, 2000), have complex patterns of stakeholders that cannot be aggregated in practice as a single and coherent customer.
53Unlike the field of industrial maintenance studies, there has been considerable research on the effects of facility management on end customer performance, typically by studying self-reported effects on office worker productivity (de Been et al., 2017). This contrasts with the limited interest in measuring the service productivity of facility management providers themselves (Bröchner, 2017).
Van der Walk and Wynstra (2014) have studied buyer-seller interaction when NS purchase cleaning services, for stations and for their own offices. They rely on business services classified into component services, instrumental and consumption services. Station cleaning and train cleaning fall within component services, while office cleaning is seen as a consumption service. This study underlines the need for mapping the complexity of seemingly mundane services and identifying differences in interaction patterns.
III. Servitization
When manufacturers offer maintenance, repair and overhaul (MRO) services in a bundle with their physical products, it is an important example of servitization, a phenomenon that has attracted considerable interest, as shown by the review articles by Kowalkowski et al. (2015) and Baines et al. (2017). Studies of the dynamic processes of servitization dominate these reviews, and only exceptionally have researchers compared bundled and unbundled MRO services from a transaction cost viewpoint – or introduced cost reasoning at all (but see e.g. Spring and Araujo, 2017). The market expansion of bundles with MRO could be partly explained by measurement cost issues and information asymmetry, insofar as servitization is often supported by an advanced analysis of equipment data, where the original manufacturer possesses historical data including data from the particular context where the equipment is used. Unique access to earlier data allows more efficient interpretation of the current flow of measurement data from a given piece of equipment.
Before the term “servitization” was coined, Otis as a leading manufacturer of lifts launched Otisline, which offered remote diagnostics 54and control for their installed lifts (Ives and Vitale, 1988; Dörner et al., 2011). Lifts are building related products, where malfunctioning is easy to observe and at the same time may pose a serious hazard. Otis and later Kone provide services that belong to both industrial maintenance and facilities management.
In his performance manifesto, outlining the trend away from just relying on financial indicators and noting inspiration from the quality movement, Eccles (1991) emphasized that “advances in information technology such as powerful workstations, open architectures, and relational databases vastly increase the options for how information can flow.” Not only the increased number of options for information flow, but also the general reduction of measurement cost due to more efficient ICT support has organizational consequences.
Today, both industrial maintenance and facility management are supported by the collection of large volumes of measurement data. In the case of facilities, it is energy management that includes generating sensor data used for the automation of indoor climate control (Zhou et al., 2016). Maglio and Lim (2016) in their analysis of big data and smart service systems introduce a fundamental distinction between data from objects and data from people. Energy use in office buildings is heavily influenced by the behaviour of office employees. As recently pointed out by an article in The Economist (April 29th, 2017)1, collecting data from office employees, directly or indirectly, raises issues of personal integrity, which should not be a challenge in the context of industrial maintenance.
If construction contractors offer packages of facility management along with their buildings (Bröchner, 2008), it is seldom labelled as servitization, although road contracts with multiyear operations and maintenance included, as well as infrastructure concessions, are to be understood as analogous phenomena. Construction contractors are project-based firms, and servitization has to be interpreted differently in this context, as illustrated by the case of construction firms developing services for energy-efficient buildings (Galera-Zarco et al., 2014). The development of information and communication technologies, in particular the Internet-of-Things based on sensors in buildings, creates 55new business opportunities for major construction contractors (Robinson et al., 2016).
Another impetus for long term servitizing of construction projects has come from government policies intended to ease the burden of public debt. From the 1990s and led by the UK, the wave of private finance projects (Winch and Schmidt, 2016) implied a quasi-integration of construction and facility management in concession consortia, although it is uncertain how far this development was driven by financial considerations and particular government policies rather than economies of service performance control.
Just like it has been observed that manufacturers who have entered a path of servitization may later abandon at least part of their service offerings (Kowalkowski et al., 2017), we find major non-service firms withdrawing from facility management; the CBRE Group acquired Global Workplace Solutions from Johnson Controls, historically a manufacturer, in 2015. Skanska, a major project development and construction group, spun off Coor Service Management already in 2004. From a performance measurement viewpoint, it is thus an open question how advances in ICT will strengthen or weaken the forces of integration.
IV. Outcome-based contracts
Many researchers have contributed in recent years to the study of outcome-based (or performance-based) contracts, often associated with industrial maintenance and servitization. Contracts based on measuring outcomes or performance are viable only if measurement is possible with little effort and ambiguity. Selviaridis and Wynstra (2015) have reviewed the literature on performance-based contracting from an operations and supply management perspective. They provide a simple model with a triangle of performance, risk and incentives. Considering that facilities management has a stronger link to supporting people in their work, rather than just upholding a technical function of equipment, it is noteworthy that the review identified numerous publications concerning the health care sector. Nevertheless, the facility management 56literature appears not to use the expression “outcome-based contracts”. As with “service triads”, the question is then whether this is merely a terminological difference or that outcome-based facility management contracts are unusual or even non-existent.
It is unlikely that the difference between industrial maintenance and facility management in this respect arises just from a generic difference in customer involvement. Ng et al. (2009) took their examples from outcome-based MRO contracts in the defence industry, emphasizing the effects of customer behaviours and involvement. In particular, they highlighted the need for understanding how customers actually use equipment, knowledge that can be translated into cost savings for both parties. The need for skills among those who deliver the services emerged as a crucial issue of human resources. Furthermore, they noted that there must be sufficient capacity to deal with situations where inspection and repair are difficult to carry out; also, that the provider depends on thorough knowledge of the customer’s capabilities when there is an element of coproduction to achieve contractual outcomes.
These observations can be interpreted in a risk management perspective. Hou and Neely (2017) now identify five dimensions of risk associated with outcome-based contracts such as are found in bundles with industrial maintenance. These dimensions are complexity, dynamism, capability, alignment and dependency. If one or more of these types of risk is excessive, outcome-based contracting is infeasible. It can be argued that “complexity” accounts for the scarcity of outcome-based facility management contracts. Incomplete descriptions of initial status of assets are more frequently met with in facility management. This deficiency can be thought of as a consequence of high costs for analysing and recording a vast set of data describing details of existing facilities. Nevertheless, for newly constructed facilities with a digital documentation inherited from the design and construction stages, there is much less uncertainty than when an external facility management service provider is brought in to manage an older building that in all probability includes previously undocumented technical changes to the structure.
The risks faced by service providers of condition-based industrial maintenance do include a limited knowledge of the initial status of assets. This is what has been highlighted by Holmström et al. (2010) who discuss visibility-based industrial services, by which they intend 57how external service providers are given access to information on the “installed base”.
Many earlier authors seem to take it for granted that outcome-based contracts are a superior solution to customers’ problems. Given the higher level of uncertainty that characterizes most facility management contracts, there might be a point in having detailed input specifications, since they might lead to constructive communication between client and provider during the contractual period (Kadefors, 2008). It is therefore crucial to consider which style of specification is more efficient in developing the capabilities of both providers and their clients.
Although there have been many studies of the effect of facility management on the perceived productivity of office workers, as mentioned in Section II.3, it is difficult to measure these effects objectively and directly, unlike productivity effects of industrial maintenance services. This could also contribute to explaining why there is little of performance contracting for facility management. One exception is what specialized energy service companies (ESCOs) offer: Energy Performance Contracting (EPC) projects, where the ESCO combines finance, installation of equipment, monitoring, staff training for system operation and control. Typically, the ESCO guarantees a level of energy savings. Clearly, and in addition to the relational risks inherent in responsibilities divided between co-producing clients and ESCOs, there are technical risks associated with measurement in EPC: “modeling errors, poor data quality for M&V works, as well as measuring imprecision” (Lee et al., 2015). It appears that measurement costs and associated risks influence or even determine the emergence and use of outcome-based contracts.
Discussion and conclusions
Over the years, research on performance measurement in industrial maintenance has moved from a single focus on technology to become more aware of organizational contexts, although these have often been restricted to the environment within an organization; there are also instances of multiple stakeholders being mentioned. Still, there is a 58strong contrast with studies of how performance is measured in facility management, which consistently appears as more customer orientated and sometimes with recognition of various categories of users of one and the same facility. This complexity of customers is probably at least one of the reasons why “service triads” is not part of the facility management researcher vocabulary. It might be doubted whether everyday practice of facility management performance measurement includes KPIs related to the productivity effects on customer core activities, but there is no lack of studies following this line of thought.
Not only “service triads” but also a major theme such as “servitization” in the field of industrial maintenance studies is a rarity in publications related to facility management performance measurement. Why “servitization” is seldom referred to by facility management researchers may reflect that facility management service providers have emerged from a variety of industry origins. A few have originated in manufacturing, typically from energy-related technologies, while the majority of facility management firms have grown from a starting point in catering, cleaning, and other business services, in addition to those who entered facility management from the construction industry. Unlike industrial maintenance, the “installed base”, which here must be interpreted as erected buildings, seldom creates a profitable link to after-sales business. It seems difficult to bridge the gap between the project culture typical of construction firms and a culture supportive of the long term contractual relations of facility management services.
While performance measurement in industrial maintenance is dominated by technology and possibly costs, the technical status of the system to be maintained appears to be easier to describe precisely than in the case of most facilities. This difference exists also for building maintenance, which is one constituent of facility management that is understandably close to industrial maintenance. Additionally, there may be less uncertainty in objectively measuring the results of industrial maintenance than in the facility management context. Both these sources of uncertainty in facility management contracts are probable reasons why an “outcome-based contract”, at least as a term, is seldom realized in facility management.
Finally, it should be noted that the differences found in the two literatures of facility management and industrial maintenance can 59appear greater than the underlying realities. Since facility management performance researchers tend to study, or at least be influenced by, how services influence people, many of them apply theories and concepts from marketing research. For those who study performance measurement in industrial maintenance, the theory background is often in operations management or supply chain management, with implications for the terminology employed. It is thus an important challenge to bridge these theoretical worlds in order to transfer ideas and experiences between facility management and industrial maintenance. There is a potential for industrial maintenance researchers to learn from facility management in order to develop the understanding of productivity effects on customers and customers’ customers; furthermore, the study of fully servitized firms rather than of the process of servitization could be inspired by facility management studies. In the opposite direction, lessons from industrial maintenance, prior studies of performance measurement for outcome-based contracts appear to hold valuable insights for facility management.
60References
Amaratunga D. & Baldry D. (2003), “A conceptual framework to measure facilities management performance”, Property Management, vol. 21, no 2, p. 171–189.
Amaratunga D., Haigh R., Sarshar M. & Baldry D. (2002), “Application of the balanced score-card concept to develop a conceptual framework to measure facilities management performance within the NHS facilities”, International Journal of Health Care Quality Assurance, vol. 15, no 4, p. 141–51.
Argyres N.S., Bercovitz J. & Mayer K.J. (2007), “Complementarity and evolution of contractual provisions: An empirical study of IT services contracts”, Organization Science, vol. 18, no 1, p. 3–19.
Baines T., Bigdeli A.Z., Bustinza O.F., Shi V.G., Baldwin J. & Ridgway K. (2017), “Servitization: revisiting the state-of-the-art and research priorities”, International Journal of Operations and Production Management, vol. 37, no 2, p. 256–278.
Barthélemy J. & Quélin B.V. (2006), “Complexity of outsourcing contracts and ex post transaction costs: an empirical investigation”, Journal of Management Studies, vol. 43, no 8, p. 1775–1797.
Barzel Y. (1982), “Measurement cost and the organization of markets”, The Journal of Law and Economics, vol. 25, no 1, p. 27–48.
Bröchner J. (2008), “Construction contractors integrating into facilities management”, Facilities, vol. 26, no 1/2, p. 6–15.
Bröchner J. (2017), “Measuring the productivity of facilities management”, Journal of Facilities Management, vol. 15, no 3, p. 285–301.
de Been I., van der Voordt T. & Haynes B. (2017), “Productivity”, in Jensen P.A. & van der Voordt T. (eds), Facilities Management and Corporate Real Estate Management as Value Drivers: How to Manage and Measure Added Value, Abingdon, Routledge, p. 140–155.
Djellal F. & Gallouj F. (2008), Measuring and Improving Productivity in Services: Issues, Strategies and Challenges, Cheltenham, Edward Elgar.
Dörner N., Gassmann O. & Gebauer H. (2011), “Service innovation: why is it so difficult to accomplish?”, Journal of Business Strategy, vol. 32, no 3, p. 37–46.
Eccles R. (1991), “The performance measurement manifesto”, Harvard Business Review, vol. 69, no 1, p. 131–137.
Featherstone P. & Baldry D. (2000), “The value of the facilities management function in the UK NHS community health-care sector”, Facilities, vol. 18, no 7/8, p. 302–311,
61Galera-Zarco C., Morales-Gallego M. & Pérez-Aróstegui M.N. (2014), “Servitization in project-based firms”, Strategic Change, vol. 23, no 5–6, p. 329–340.
Hinks J. & McNay P. (1999), “The creation of a management-by-variance tool for facilities management performance assessment”, Facilities, vol. 17, no 1/2, p. 31–53.
Holmström J., Brax S. & Ala-Risku T. (2010), “Comparing provider-customer constellations of visibility-based service”, Journal of Service Management, vol. 21, no 5, p. 675–692.
Hou J. & Neely A. (2017), “Investigating risks of outcome-based service contracts from a provider’s perspective”, International Journal of Production Research, doi: 10.1080/00207543.2017.1319089.
Ives B. & Vitale M.R. (1988), “After the sale: leveraging maintenance with information technology”, MIS Quarterly, vol. 12, no 1, p. 7–21.
Jaakkola E., Meiren T., Witell L., Edvardsson B., Schäfer A., Reynoso J., Sebastiani R. & Weitlaner D. (2017), “Does one size fit all? New service development across different types of services”, Journal of Service Management, vol. 28, no 2, p. 329–347.
Jensen P.A. (2017), “Strategic sourcing and procurement of facilities management services”, Journal of Global Operations and Strategic Sourcing, vol. 10, no 2, doi: 10.1108/JGOSS-10-2016-0029.
Kadefors A. (2008), “Contracting in FM: collaboration, coordination and control”, Journal of Facilities Management, vol. 6, no 3, p. 178–188.
Kadefors A. & Bröchner J. (2004), “Building users, owners and service providers: new relations and their effects”, Facilities, vol. 22, no 11/12, p. 278–283.
Karatzas A., Johnson M. & Bastl M. (2016), “Relationship determinants of performance in service triads: a configurational approach”, Journal of Supply Chain Management, vol. 52, no 3, p. 28–47.
Kowalkowski C., Windahl C., Kindström D. & Gebauer H. (2015), “What service transition? Rethinking established assumptions about manufacturers’ service-led growth strategies”, Industrial Marketing Management, vol. 45, p. 59–69.
Kowalkowski C., Gebauer H., Kamp B. & Parry G. (2017), “Servitization and deservitization: Overview, concepts, and definitions”, Industrial Marketing Management, vol. 60, p. 4–10.
Kumar U., Galar D., Parida A., Stenström C. & Berges L. (2013), “Maintenance performance metrics: a state-of-the-art review”, Journal of Quality in Maintenance Engineering, vol. 19, no 3, p. 233–277.
Lacity M.C., Willcocks L.P. & Khan S. (2011), “Beyond transaction cost 62economics: towards an endogenous theory of information technology outsourcing”, Journal of Strategic Information Systems, vol. 20, no 2, p. 139–157.
Lai A.W. & Pang P.S. (2010), “Measuring performance for building maintenance providers”, Journal of Construction Engineering and Management, vol. 136, no 8, p. 864–876.
Lai J.H. & Choi E.C. (2015), “Performance measurement for teaching hotels: A hierarchical system incorporating facilities management”, Journal of Hospitality, Leisure, Sport and Tourism Education, vol. 16, p. 48–58.
Langlois R.N. (1992), “Transaction-cost economics in real time”, Industrial and Corporate Change, vol. 1, no 1, p. 99–127.
Lavy S., Garcia J.A. & Dixit M.K. (2010), “Establishment of KPIs for facility performance measurement: review of literature”, Facilities, vol. 28, no 9/10, p. 440–464.
Lay G., Schroeter M. & Biege S. (2009), “Service-based business concepts: A typology for business-to-business markets”, European Management Journal, vol. 27, no 6, p. 442–455.
Lee P., Lam P.T.I. & Lee W.L. (2015), “Risks in energy performance contracting (EPC) projects”, Energy and Buildings, vol. 92, p. 116–127.
Maglio P.P. & Lim C.H. (2016), “Innovation and Big Data in Smart Service Systems”, Journal of Innovation Management, vol. 4, no 1, p. 11–21.
Meng X. & Minogue M. (2011), “Performance measurement models in facility management: a comparative study”, Facilities, vol. 29, no 11/12, p. 472–484.
Muchiri P.N., Pintelon L., Martin H. & De Meyer A.M. (2010), “Empirical analysis of maintenance performance measurement in Belgian industries”, International Journal of Production Research, vol. 48, no 20, p. 5905–5924.
Ng I.C., Maull R. & Yip N. (2009), “Outcome-based contracts as a driver for systems thinking and service-dominant logic in service science: Evidence from the defence industry”, European Management Journal, vol. 27, no 6, p. 377–387.
Nguyen T.A. & Aiello M. (2013), “Energy intelligent buildings based on user activity: A survey”, Energy and Buildings, vol. 56, p. 244–257.
Parida A., Kumar U., Galar D. & Stenström C. (2015), “Performance measurement and management for maintenance: a literature review”, Journal of Quality in Maintenance Engineering, vol. 21, no 1, p. 2–33.
Pekkola S., Saunila M., Ukko J. & Rantala T. (2016), “The role of performance measurement in developing industrial services”, Journal of Quality in Maintenance Engineering, vol. 22, no 3, p. 264–276.
Robinson W., Chan P. & Lau T. (2016), “Finding new ways of creating value: A case study of servitization in construction”, Research-Technology Management, vol. 59, no 3, p. 37–49.
63Selviaridis K. & Wynstra F. (2015), “Performance-based contracting: a literature review and future research directions”, International Journal of Production Research, vol. 53, no 12, p. 3505–3540.
Simões J.M., Gomes C.F & Yasin M.M. (2011), “A literature review of maintenance performance measurement: A conceptual framework and directions for future research”, Journal of Quality in Maintenance Engineering, vol. 17, no 2, p. 116–137.
Siu G.K.W., Bridge, A. & Skitmore R.M. (2001), “Assessing the service quality of building maintenance providers: mechanical and engineering services”, Construction Management and Economics, vol. 19, no 7, p. 719–726.
Spring M. & Araujo L. (2017), “Product biographies in servitization and the circular economy”, Industrial Marketing Management, vol. 60, p. 126–137.
Toossi A., Lockett H.L., Raja J.Z. & Martinez V. (2013), “Assessing the value dimensions of outsourced maintenance services”, Journal of Quality in Maintenance Engineering, vol. 19, no 4, p. 348–363.
Tsang A.H.C., Jardine A.K.S. & Kolodny H. (1999), “Measuring maintenance performance: a holistic approach”, International Journal of Operations & Production Management, vol. 19, no 7, p. 691–715.
Tucker M. & Smith A. (2008), “User perceptions in workplace productivity and strategic FM delivery”, Facilities, vol. 26, no 5/6, p. 196–212.
van der Valk W. & Wynstra F. (2014), “Variety in business-to-business services and buyer-supplier interaction: The case of cleaning services”, International Journal of Operations and Production Management, vol. 34, no 2, p. 195–220.
van der Valk W. & van Iwaarden J. (2011), “Monitoring in service triads consisting of buyers, subcontractors and end customers”, Journal of Purchasing and Supply Management, vol. 17, no 3, p. 198–206.
Winch G.M. & Schmidt S. (2016), “Public-Private Partnerships: A review of the UK Private Finance Initiative”, in Jefferies M.C. & Rowlinson S. (eds), New Forms of Procurement: PPP and Relational Contracting in the 21st Century, Abingdon, Routledge, p. 35–51.
Wynstra F., Spring M. & Schoenherr T. (2015), “Service triads: A research agenda for buyer–supplier–customer triads in business services”, Journal of Operations Management, vol. 35, p. 1–20.
Zhou K., Fu C. & Yang S. (2016), “Big data driven smart energy management: From big data to big insights”, Renewable and Sustainable Energy Reviews, vol. 56, p. 215–225.
1 ”The office of tomorrow: Sofas and surveillance”, The Economist, April 29th, p. 57–58.